![]() |
> E&O/GL Insurance for Home Inspectors Competitive Rates, Broad Coverage, Free Risk Management, online inspection support for tough questions, discounts on education and more... |
>> Editor’s Note: To help you stay up-to-date and connected, OREP/Working RE has established a Coronavirus (COVID-19) Discussion and Resource Page where you can share your thoughts, experiences, advice and challenges with fellow inspectors. See what Inspectors are saying here!
Air Conditioning Basics / Inspection: The Science Behind Your Inspection
By Tom Feiza, Mr. Fix-It, Inc. HowToOperateYourHome.com
Air Conditioning Basic Systems and Inspection Standards
Home inspectors should follow national standards when visually inspecting a residential air conditioning system. Most standards require opening readily accessible panels or panels that a typical home owner would open. Standards require inspection of central and permanently installed cooling equipment and distribution systems. Standards also require a description of the energy source and cooling systems.
While the standards are pretty open to the level and type of inspection required, all home inspectors will do a better inspection if they understand the science behind a typical residential air conditioning system. I will focus on explaining a typical air conditioning system combined with a forced air furnace distribution (fan coil) as shown in Figure 1.
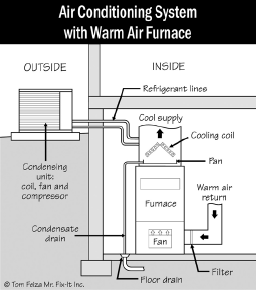
Refrigeration System Basics and What is a Ton of Cooling?
Ever hear of a two-or three-ton central air conditioner? Does that mean a two-ton air conditioner weighs 4,000 pounds? Is the term related to cooling capacity, or is it a random term that tech folks use to impress us? We all know the answers—right?
A Two Ton AC Unit Does Not Weigh 4,000 Pounds
A ton is a unit of refrigeration/cooling capacity used in the U.S. A ton of cooling is the equivalent to transferring 12,000 Btu of energy per hour. So, a ton of air conditioning removes 12,000 Btu from the air of a home in one hour—cooling the air. A 4–ton unit removes 48,000 Btu.
You might know how to look at the nameplate of the exterior condenser/compressor AC unit and read the rated tons of cooling coded in the model number. The tag may also list the tons of cooling capacity.
Where did “Ton” Originate?
When engineer Joe Cool (at least I think “cool” was part of his name) developed the standards for measuring mechanical cooling, ice was commonly used for cooling. You know, in the old days, food was stored in the ice cooler, and there was no air conditioning. Ice was delivered to homes for the “ice box”. So, Joe decided that the cooling capacity measurement should relate to ice (See Figure 2).
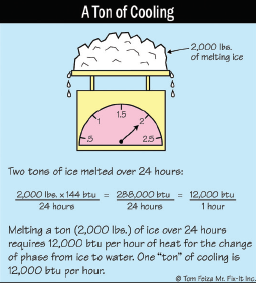
A standard was set equating one “ton” of cooling to the amount of energy needed to melt one ton (2,000 lbs.) of ice over a 24–hour period. With the change of phase from ICE to WATER, 144 Btu of latent energy is required. 2000 pounds times 144 Btu/lb. = 288,000 Btu. 288,000 Btu over 24 hours is 12,000 Btu/hour—or a one “TON” rating.
Btu – British Thermal Unit
So, what is a Btu? It stands for British thermal unit, the amount of energy needed to raise the temperature of one pound of water one degree Fahrenheit at standard temperature and pressure. A reasonable equivalent is the energy you get from completely burning one kitchen match. So, a “ton” of cooling (or heating) transfers 288,000 Btu—equivalent to about 288,000 kitchen matches of energy (See Figure 3).
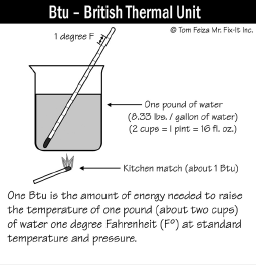
OK? What Transfers the “Ton” of Energy in Air Conditioning?
For residential air conditioning, two coils, a compressor and a control/metering device is used to mechanically transfer heat. (See Figure 4). The refrigerant vapor is compressed and then cooled/condensed into a liquid in the outside unit. The liquid evaporates/boils in the “A” coil in the interior ductwork with the energy from the warm air circulated over the coil. The interior warm air is cooled as it passes through the “A” coil and back into the home.
Outside A Home—Compressor and Condenser Outside you are familiar with what we call the compressor and or condenser unit (See Figure 1, and Figure 7). This unit is manufactured with a copper fin coil wrapped around a refrigerant compressor. A fan is mounted on the top of the unit. The compressor is only visible if you look inside through the grill.
Figure 7 shows two compressor/condensers. The one on the left is for the typical air conditioning system we are discussing here. The white unit on the right is for a direct expansion unit that can have multiple coils/fans mounted in several room (See Figure 4).
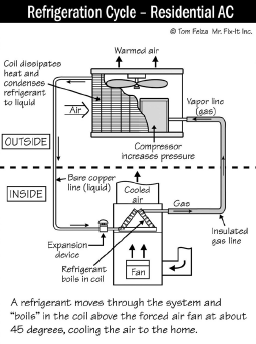
Refrigerant vapor (R12, R22, R134) flows from the A coil inside the home to the external compressor. The compressor may be a piston type just like a piston and crank shaft on a single cylinder lawn mower engine. Newer units often use a scroll compressor (See Figure 6) which is more like a centrifugal compressor. The compressor changes the low pressure refrigerant vapor into high pressure refrigerant vapor and moves it into the exterior condenser coil.
The exterior coil with fins, remove heat from the high pressure refrigerant and “condense” the vapor back into a liquid refrigerant. The fan moves a large quantity of exterior air over the coil to transfer the heat from the refrigerant to the exterior air.
The cooling or refrigeration system is a sealed system and when operating properly it should never lose refrigerant. Today all units are moving away from the old Freon (R12, R22) type of hydrocarbon refrigerant because of potential damage to the ozone in the atmosphere.
(story continues below)
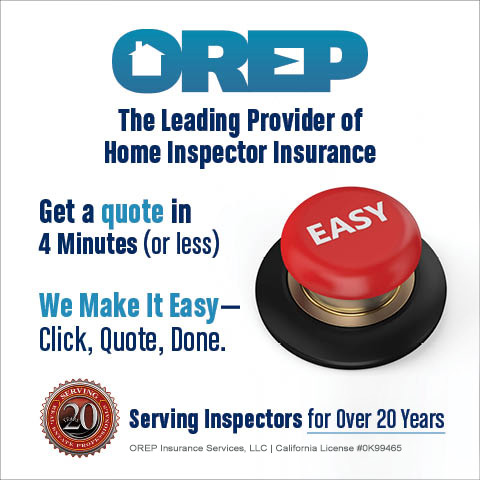
Inside a Home—Meter and “A” Coil
The liquid refrigerant now moves from the exterior to the forced air furnace and a metering device just before the “A” coil—refer to Figure 4. The “A” coil is depicted in Figures 1 and 4 and an actual coil is shown in Figure 8. Home inspector rarely sees an actual A-coil because they are hidden in metal ductwork.
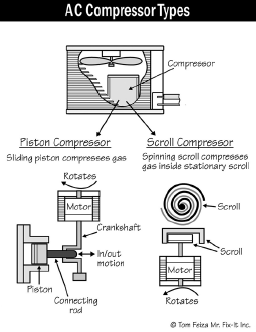
The forced air furnace or fan-coil system has a carefully engineered metering device, specific blower fan capacity, specific coil capacity and a duct system designed to deliver just the right amount of refrigerant and air to cause the refrigerant to “boil” in the A-coil.
As the refrigerant “boils” in the A-coil, warm home air is pushed across the coil and is cooled. Typically, the temperature of the inside air drops 14 to 22 degrees Fahrenheit moving across the coil. Some home inspectors measure this air temperature before and after the A-coil to determine the “delta T” or temperature drop across the coil. If the air flow is reduced, say with a plugged air filter, the coil could freeze up.
Inside Condensation—Water Issue
The home air is typically cooled below the dew point temperature and condensation occurs on the A-coil. This condensation is caught in a pan below the coil and drained by gravity outside the furnace/ductwork. Every air conditioning system has a condensate drain. You can see the black plastic pan below the coil in Figure 8. The drain connections on the lower left of the pan. Normally only the low drain connection is used.
Your Inspection Inside
For the inspection, you should always note any water leaks or signs of water leaks below the A-coil. Any signs of leaks at the furnace/ductwork require further investigation. Leaks cause extensive damage to electronic components of the furnace. Check the drain lines to be sure they are draining properly to a suitable floor drain. You may want to measure the temperature drop across the coil.
When the evaporator coil/furnace/fan system is located in an attic above a living space (See Figure 8) leaks can be a huge issue. This type of system should have a secondary pan below the unit with a separate drain. A water alarm system in the pan is also a good idea. Leaks from this type of system can be very damaging to the structure and dry-wall in a home.
Your Inspection Outside
The compressor/condenser outside should be level and clean as shown in (See Figure 6). Often the compressor and pad tips over time and can put tension on the refrigeration lines. If the unit is not level, this can also cause a lubrication issue.
There should be at least 12 inches of clearance around the coils and 3-feet of clearance at the fan discharge. Take a close look at the fins/coils—they should be clean. At times a bright flashlight helps inspect the fine fins on the coils behind the grills. Fins are often blocked with lint and dirt.
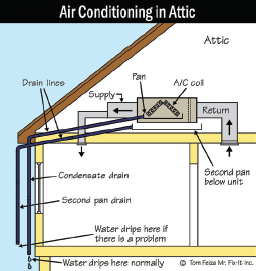
I have included an example (See Figure 9) showing how the exterior coil and fins can be damaged. Do you think they have a large dog at this home?
Outside (See Figure 7) there should be an exterior electrical disconnect for servicing the unit. Some inspectors will also check the amp rating of the unit and check to make sure the overload breaker or fuse is sized correctly. The breaker may be in the exterior disconnect or in the main electrical panel of the home and it will always be 240 volt.
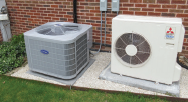
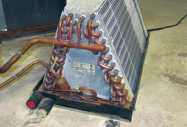
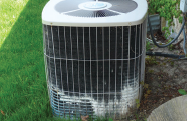
The Takeaway
Inspectors should understand the basic science and engineering behind a residential air conditioning system. I have explained the basics—but there are many variables with different types of systems. If you understand a basic refrigeration cycle, you are good. Note: a modern refrigerator has all the same components.
When you identify an AC unit as 3 Ton from the nametag designation, you know the equivalent is melting 3 tons of ice in 24 hours or 36,000 Btu per hour. Use this to impress your clients and so you both understand that “Ton” of cooling.
About the Author
Tom Feiza has been a professional home inspector since 1992 and has a degree in engineering. Through HowToOperateYourHome.com, he provides high-quality marketing materials, books for homeowners, and illustrations that help professional home inspectors educate their customers. Copyright © 2022 by Tom Feiza, Mr. Fix-It, Inc. Reproduced with permission.
Visit HowToOperateYourHome.com (or htoyh.com) for more information about building science, books, articles, marketing, and illustrations for home inspectors. E-mail Tom (Tom@htoyh.com) with questions and comments, or phone (262) 303-4884.
OREP/WRE Coronavirus Discussion and Resource Page Coronavirus: National Home Inspector Survey
Real-Life Inspector Lawsuits and How to Protect Yourself Available Now Presenter: Isaac Peck, President of OREP Isaac Peck, President of OREP Insurance Services, shares his insights and advice gained over nearly 10 years of providing risk management and E&O insurance for home inspectors. You will not hear many of these insights anywhere else. Watch Now!
Send your story submission/idea to the Editor: isaac@orep.org
Note: The Summer 2022 Working RE Home Inspector is now mailing to over 25,000 home inspectors nationwide. OREP Insureds/members enjoy guaranteed delivery of each print magazine and many more benefits.
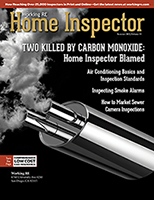